The pultrusion process involves pulling resin-impregnated glass fiber materials through a die. The materials can be bundles, tapes, or fabrics. They shape and cure the materials to create FRP profiles of unlimited length. This process is particularly suitable for manufacturing FRP profiles of various cross-sectional shapes, such as FRP rods, FRP pultruded round tubes, solid profiles (FRP H-beams, FRP U-channels, FRP angles, FRP I-beams), and hollow profiles (window and door profiles, blades, etc.).
The pultrusion process is a special composite material-forming technique.
Advantages:
The production process is fully automated, ensuring high efficiency.
Pultruded products can have up to 80% fiber content. The impregnation occurs under tension. This maximizes the fibers’ reinforcing effect and results in high strength.
You can adjust the products’ strengths to meet different needs.
The process creates no waste. The products need no post-processing. This saves labor, raw materials, and energy compared to other processes.
The product has stable quality, good repeatability, and cuts to any length.
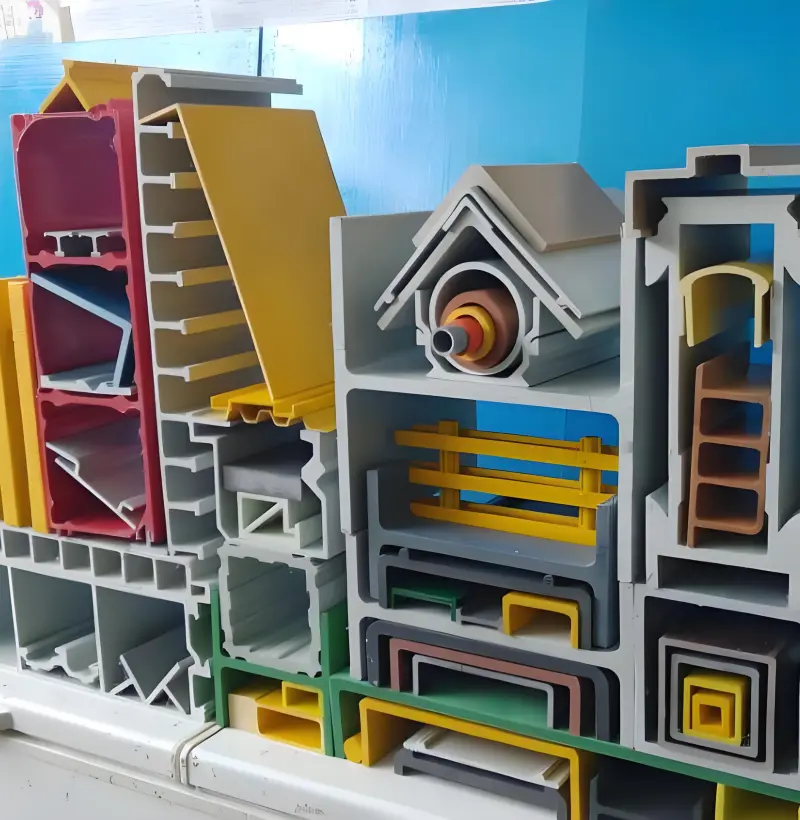
FRP profiles
The pultrusion process has some drawbacks. It can only make linear shapes. Also, it has low transverse strength.
(1) Raw materials for pultrusion
Resin matrix: Over 90% of pultrusion uses unsaturated polyester resin. It is the most used resin in this process. Other resins are epoxy, vinyl ester, thermosetting methacrylic, modified phenolic, and flame-retardant.
Reinforcing materials: Pultrusion mainly uses glass fibers. These include products like untwisted roving and continuous fiber mats. You can also select aramid, carbon, and metal fibers to meet special performance needs. Regardless of the type of fiber, we must treat their surface to ensure good adhesion to the resin matrix.
③ Auxiliary materials: The auxiliary materials for pultrusion mainly include release agents and fillers.
(2) Pultrusion molds
Molds are key tools in pultrusion. They usually include a pre-forming mold and a forming mold.
- Pre-forming mold: In pultrusion, the reinforcing materials must be resin-impregnated. They must then pass through a pre-forming mold and some guides before entering the forming mold. The pre-forming mold’s job is to shape the resin-soaked fibers into a pre-form. This pre-form must match the shape and size of the forming mold. It ensures uniform fiber content in the product’s cross-section.
2. Forming mold: The mold’s cross-sectional area should be at least 10 times that of the product. This ensures the mold’s strength and rigidity. It also ensures stable, uniform heat distribution after heating. The pultrusion mold length depends on the pulling and resin curing speeds. It must ensure the product is ready for demolding when pulled out. The mold is usually steel with chrome plating. Its cavity surface must be smooth and wear-resistant. This will reduce friction during pultrusion and extend the mold’s life.
(3) Pultrusion process
The pultrusion process has several steps: fiber feeding, resin impregnation, pre-forming, curing and shaping, pulling, and cutting. The roving frame draws untwisted roving. It passes through a fiber guide, then enters a resin bath to be fully impregnated with resin. It then enters the pre-forming mold to expel excess resin and air bubbles. After that, it enters the forming mold for gelation and curing. A pulling machine continuously removes the cured product from the mold. A cutting machine then cuts it to the desired length. You can carry out each step in the process using different methods. For example, in the fiber feeding step, add continuous fiber mats, helical winding fibers, or triaxial fabrics. They will improve the product’s transverse strength. A crawler-type traction machine or a mechanical hand can perform the traction process. The curing method can be in-mold curing or curing in a heating furnace. The heating method can be high-frequency electric heating or molten metal heating.
(4) Other pultrusion-molding processes.
Besides vertical and horizontal units, there are also processes for:
Curved products
Reaction injection pultrusion
Pultrusion with fillers.
Scan the QR Code with WeChat