1. Poor quality control of raw materials.
Raw materials are the cornerstone of the quality of fiberglass profiles. Key raw materials, such as resin, glass fiber, fillers, and curing agents, affect how well the product performs. Impurities, excess moisture, weak materials, or large batch differences can cause production issues. This may cause defects like cracks, bubbles, and weak profiles. We need to conduct a thorough screening and control of raw materials. This will help avoid product quality problems.
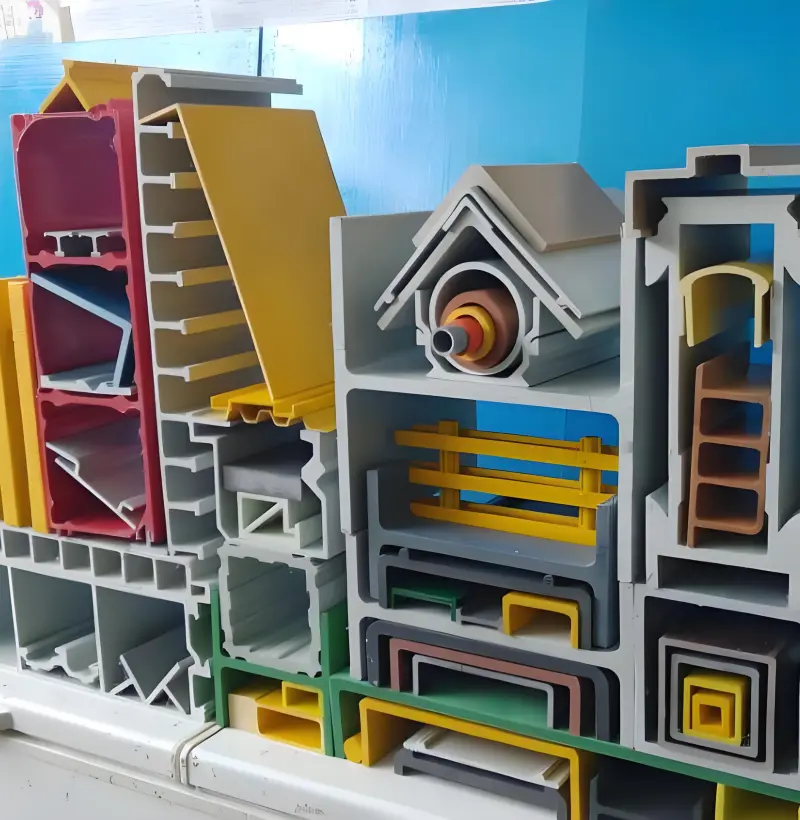
problems in fiberglass profiles
2. Outdated production processes and technological levels.
Production technology and its level are key factors in the quality of FRP profiles. Some manufacturers face challenges due to old equipment and outdated technology. It’s hard to control key factors like temperature, pressure, and time in production. They often face problems like incomplete curing, poor dimensions, and low surface quality. Weak quality control systems and testing methods make it hard to find and fix problems on time.
3. Unreasonable formula design
The design of fiberglass profiles uses a mix of components. This includes resin, reinforcement materials, fillers, and curing agents. The right ratio of these parts is key to the formula. A good formula design can maximize the strengths of each part. This boosts the product’s performance. If the formula design is off, problems can arise. For example, using the wrong resin or curing agents can hurt product performance. Imbalanced filler ratios and uneven distribution of reinforcing materials also lead to problems. This can lead to issues like weak strength, low toughness, and poor weather resistance.
4. Poor production management
Production management is an important link in ensuring stable product quality. A company needs a good production management system. Without it, issues can arise. Poor planning, weak process control, and no quality tracking can cause low efficiency and major quality shifts. Low skill levels and poor employee operations cause many product quality issues.
5. Environmental impact and improper post-treatment.
The production and use of fiberglass profiles are also affected by environmental factors. For example, changes in temperature, humidity, and UV radiation can harm product performance. We must control post-processing steps like cutting, polishing, and painting. If not, they can damage the surface and create uneven color. If companies ignore these environmental factors and post-treatment processes, product quality will worsen.
Conclusion
In summary, fiberglass profile quality issues arise from several factors. These include raw materials, production processes, formula design, production management, and environmental influences.
To improve fiberglass profiles, companies should focus on a few key areas:
Control the quality of raw materials from the start.
Use advanced production processes and technologies.
Optimize formula design.
Create a strong production management system.
Check environmental changes and manage post-treatment processes.
This is the best way to fix fiberglass profile quality issues. It will also help the industry grow and develop further.
Scan the QR Code with WeChat